SEE HOW BMW LEADS THE WAY IN HIGH-TECH AUTOMOTIVE MANUFACTURING
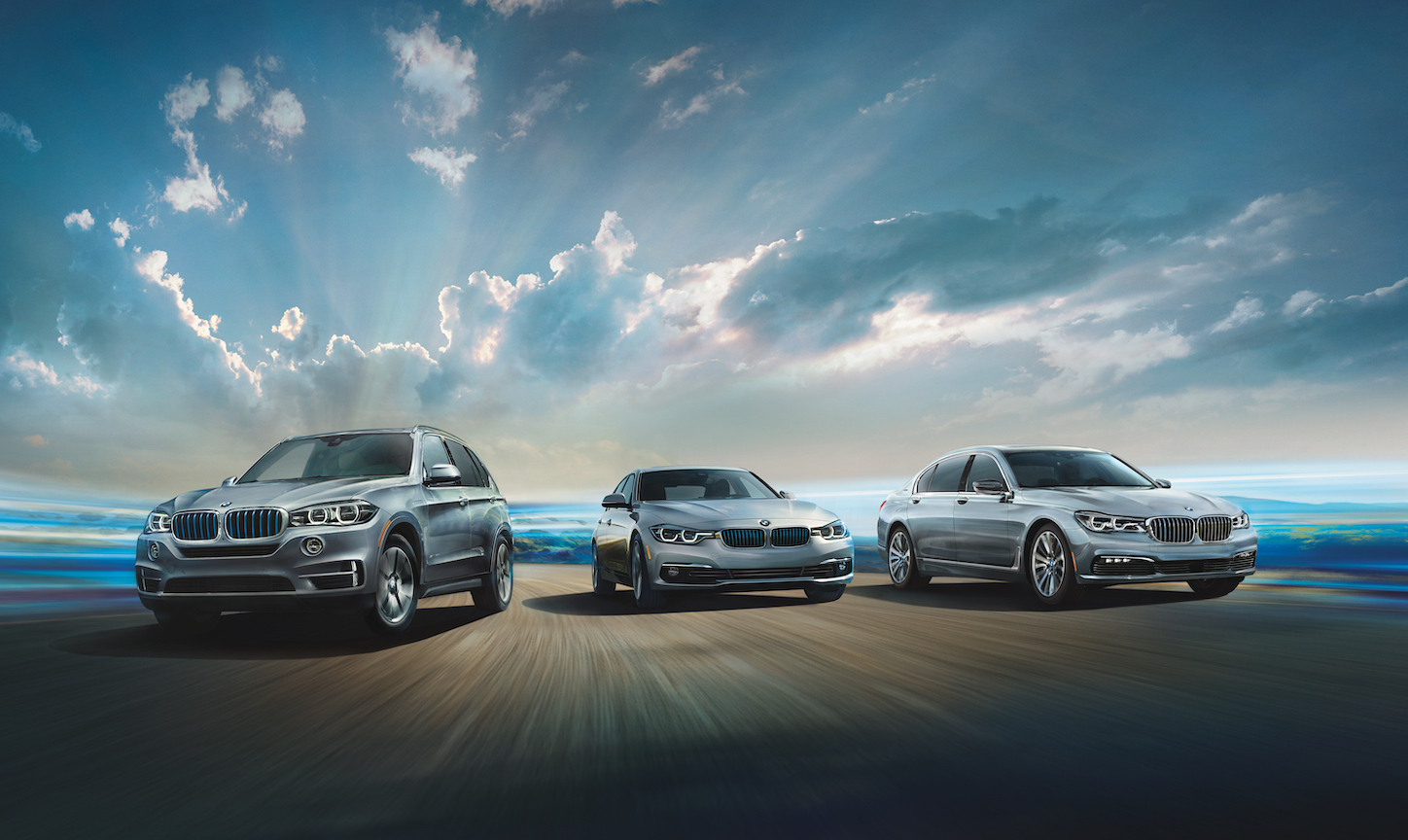
Many people know that BMW makes some of the finest automobiles in the world, using generations of knowledge that has made German engineering and craftsmanship a high standard for the rest of the industry. However, many people may not be aware of the cutting-edge innovations currently in use in the brand’s manufacturing network, and even more surprising, that many of those innovations have been introduced right here in the United States at the state-of-the-art BMW Group Plant Spartanburg in South Carolina (pictured below).
Robotics
BMW tested out one of its first autonomous manufacturing robots in the Spartanburg plant a few years ago. This lightweight robot started out its career with a very technical-sounding name, but the Spartanburg crew eventually came to call it Miss Charlotte, in honor of the nearby metropolis. Miss Charlotte worked independently mounting soundproofing to the plant’s countless doors. Today, dozens of these autonomous machines work independently on various tasks at BMW Group plants around the world.
These robots can perform tasks that may be particularly strenuous or otherwise difficult to perform for humans. For example, one ceiling-mounted lightweight robot in the BMW Group Plant Dingolfing works tirelessly every day in the axle transmission assembly area, lifting heavy bevel grates and fitting them with great precision. Even though these machines can perform tasks humans cannot, they still work “hand in hand” with their human counterparts. The machines can sense humans nearby and take precautions to slow their movement to avoid the risk of injuries.
Machines like this not only have the benefit of efficiency and precision; they also have the added benefit of freeing up human workers for other tasks that require critical thinking and creativity.
Exoskeleton Suits
But not all of the robotics can work autonomously. BMW manufacturing staff are also using some of the world’s first exoskeleton suits in everyday tasks along the assembly line. The suits use the same mechanics as robots, but they fit around a human’s body like a suit, providing added strength and support for strenuous activities, like heavy lifting or other prolonged work.
Dozens of workers in the Spartanburg plant use the upper-body versions of these exoskeleton suits (pictured above) to lift heavy parts into place for assembly, while staff in some of the German plants use the lower-body suits as convenient chairs for tasks that require frequent moving in lower positions. Imagine just sitting in place without the need to find or move a chair around each time. At the end of the workday, these suits come off just like any kind of safety harness.
Google Glass
The BMW Group Spartanburg Plant also houses some of the automaker’s pre-series testing for upcoming models still in development. Designers and engineers there use Google Glass (pictured below), wearable computers that fit just like a pair of glasses. With these, test engineers can easily record and document their testing procedures. It’s simply more convenient, but it also adds more detailed data to use in later analyses, ultimately resulting in greater precision in developing the highest-quality products for consumers.
Industry 4.0
The over-arching ethos behind much of this development is what the manufacturing world calls “Industry 4.0.” The term describes the modern movement to evolve manufacturing technology to an entirely digital framework that can easily think for itself, learning and adapting along the way. If the first three “versions” of the manufacturing industry evolved along mechanical power, then assembly line production, and finally to computerized machinery, then this “version 4.0” is all about Artificial Intelligence (AI).
BMW envisions a future where AI creates greater flexibility in manufacturing automobiles. Not only will this new technology make the assembly process more efficient, precise, and safe; but it will also mean the process can adapt to changes more easily. No longer will an assembly line be stuck to a specific model design for years. A more flexible method will mean that model updates can be added to production quickly with little added cost, resulting in the automaker’s ability to provide consumers with the most technologically updated models on the road.
Are you ready to see how all of this advanced technology results in BMW’s world-class automobiles? We would love to show you. Check out our extensive inventory of new luxury models, many of them made right here in the US with talented workers using high-tech machinery. When you’re ready to experience it in person, contact our sales staff online to schedule a test drive.
Image Credit: BMW Marketing Central